SCRAP PROCESSING SOLUTIONS
Capable of handling incredible surges and demands, yet able to keep running reliably and continually for years, General Kinematics Scrap Processing Solutions just keeps going. Starting with the rugged design of the UMO for extreme impacts, surges, and large capacities to the turbocharged High Stroke Feeder for enhanced performance in optical sorting technology, GK’s vibratory equipment fills the void in the scrap processing industry.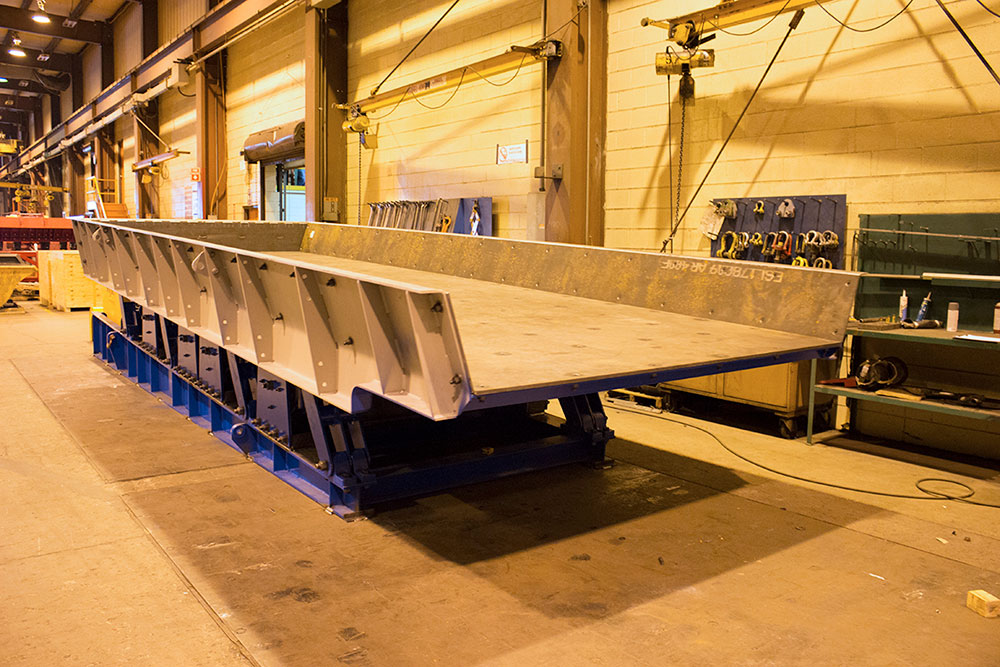
UNDER MILL OSCILLATORS
As the first piece of equipment following the shredder, an Under Mill Oscillator (UMO) is an integral machine that is required to be dependable, reliable and rugged enough to handle the high impacts and process flow demands from the shredder.
General Kinematics UMO’s are designed with extra structural and gridwork reinforcement to ensure trough integrity that will withstand the severe conditions found underneath auto-shredders. In addition, GK’s UMO’s provide consistent conveying throughout various surge loads. Specifically engineered for this application, combining GK’s SYNCRO-SHEAR® with the SYNCRO-CUSHION™ Drive assembly provides lateral stability and downstops to handle the force of even the largest explosions without damage to the conveyor.
GK frequently works with system integrators around the world to provide the best solution for the most challenging applications. GK’s Under Mill Oscillators have proven reliability and performance, with installations still in operation for over twenty years. Call us to upgrade or replace your existing UMO.
Extra thick trough liners in the impact areas.
Flared trough designs to minimize jamming and provide better flowability.
Structural downstops to prevent over-stroke of trough from overloading, explosions, or heavy impacts.
SYNCRO-SHEAR® spring system to provide lateral stability in all phases of operation.
Rear mounted SYNCRO-CUSHION™ Drive for reliability and ease of access.
Convenient, centralized lubrication access for routine maintenance of bearings.
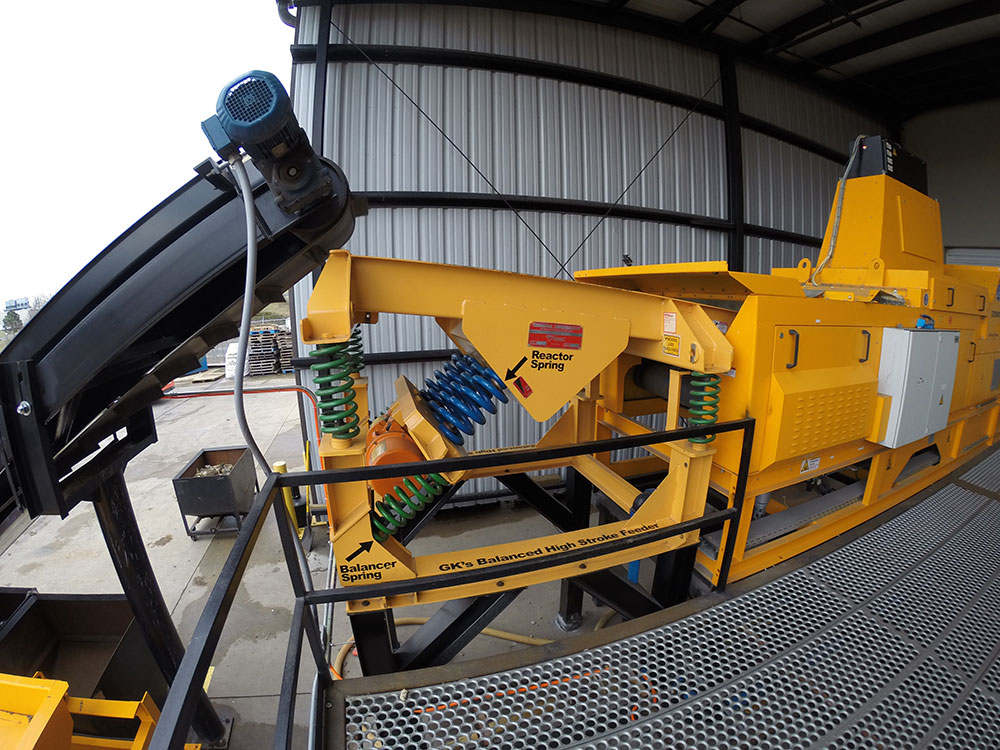
GK’S HIGH STROKE VIBRATING FEEDER
Cutting edge vibratory technology for enhanced material presentation
Challenged by our customers to do more within a limited footprint, General Kinematics developed the High Stroke Feeder (HSF) to create separation, improve on purity / recovery and increase the bottom line. GK’s HSF vibratory feeders improve on the presentation and recovery of various commodities by putting more energy into the material, thereby increasing separation of the various particles. In addition this spreads the materials across the width of the unit thereby resulting in enhanced material presentation for your optical sorter. General Kinematics has redefined the synergy between vibratory feeders and optical sorters.
High Stroke Creates Separation for Improved Purity
Faster Travel Speed = Better Material Separation = Optimal Recovery
More Energy Transmitted To the Material
Full Width Spread in Shorter Length
Lower Initial and Operating Costs
Dynamic Response to Negate Surge Loads
Up to 2/3 Less HP required to operate
OPTIONAL HSF FEATURES:
Specifically Engineered For the Industry
Optional Balanced Design Base
OEM Specific Models
Foot, Suspension or Combination Mounted Models
Mild Steel, Stainless Steel, Abrasion Resistant Steel Construction
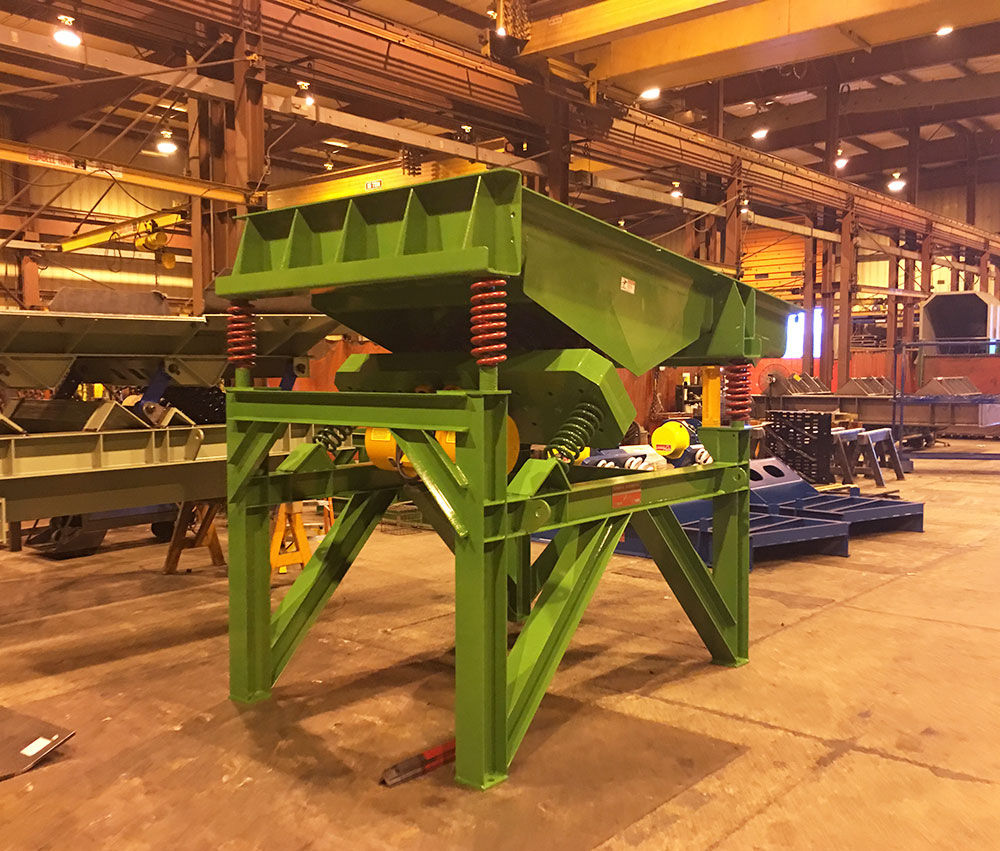
HD-HSF: HIGH DISPLACEMENT HIGH STROKE FEEDER
The latest vibratory technology for enhanced material presentation Challenged again by our customers to do more within a limited footprint, General Kinematics has pushed the limits further and developed a High Displacement-High Stroke Feeder (HD-HSF) to create more separation, enhance purity levels, improve recovery and increase your bottom line. GK’s HD-HSF vibratory feeders improve the presentation of materials and recovery of various commodities by putting more energy into the material, thereby increasing separation of the various particles. In addition, this spreads the materials across the width of the unit thereby resulting in enhanced material presentation for your optical sorter. General Kinematics has redefined the synergy between vibratory feeders and optical sorters.
HD-HSF PERFORMANCE ADVANTAGES:High Stroke Creates Separation for Improved Purity
Faster Travel Speed = Better Material Separation = Optimal Recovery
More Energy Transmitted To the Material
Full Width Spread in Shorter Length
Lower Initial and Operating Costs
Dynamic Response to Negate Surge Loads
Up to 2/3 Less HP required to operate
OPTIONAL HD-HSF FEATURES:
Specifically Engineered For the Industry
Optional Balanced Design Base which means no additional support structural work is required, thereby providing the best control, distribution and containment of materials
OEM Specific Models
Foot, Suspension or Combination Mounted Models
Mild Steel, Stainless Steel, Abrasion Resistant Steel Construction
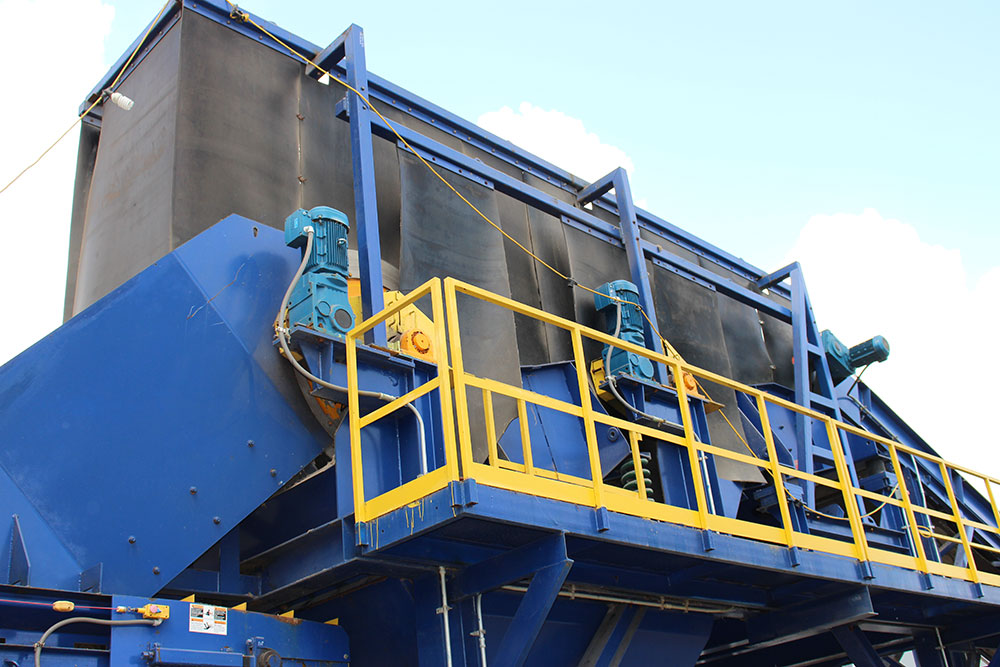
DRUM MAGNET FEEDERS & CONVEYORS
General Kinematics Drum Magnet Feeders and Conveyors are designed for the most challenging applications. GK’s Two-Mass Vibratory Feeders dynamically compensate for surge loadings to provide uniform feed to the drum magnet. Learn more about how Two-Mass works here.
GK’s Vibratory Conveyors provide a higher stroke for maximum material movement, increased travel speed and uniform displacement across the trough.
General Kinematics specializes in Custom Two-Mass Feeders and Conveyors that are creative solutions with tight tolerances or difficult installations. Customers around the world have been impressed with GK’s ability to engineer and manufacture solutions that the competition simply can’t.
Rugged design to handle heavy impacts without slowing down.
Creative solutions with tight tolerances or difficult installations.
Dynamically compensate for varying load conditions, assuring full, non-dampening performance
Energy saving natural frequency drive produces a high stroke using one low rpm motor.
Isolation mounts reduce dynamic load transmission to support structure.
More energy transmitted to the material.
Full width spread in shorter length.
Lower initial and operating costs.
Single Deck, Double Deck units available.
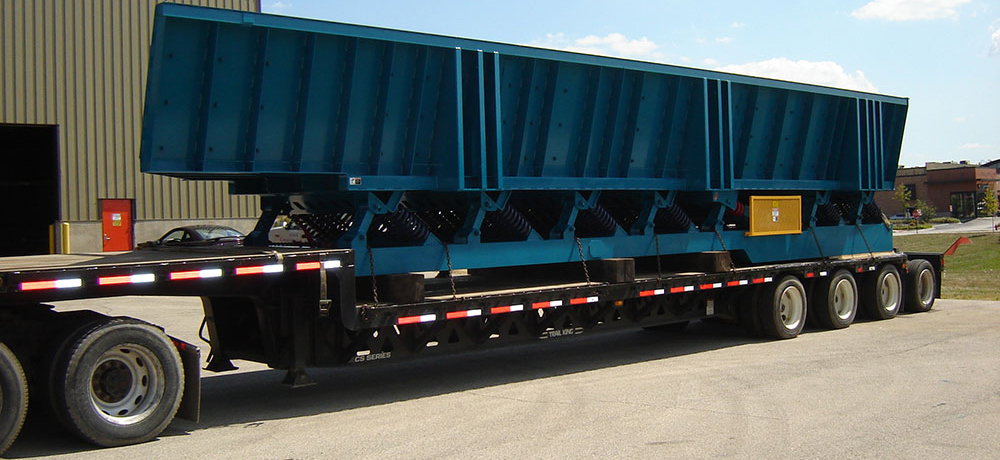
ASR METERING FEEDER
Re-feed your ASR downstream with General Kinematics’ ASR Metering Feeder. Extra large capacity allows maximum resonance time between loads. Flared trough, deep sides and a controlled discharge allow metering capabilities to be utilized. Combined with a feed back loop to a VFD, will give you ultimate control of your ASR feed rate.
FEATURES:Extra large capacity.
VFD control for a metered and consistent feed rate.
Two-Mass design, for low horsepower requirements.
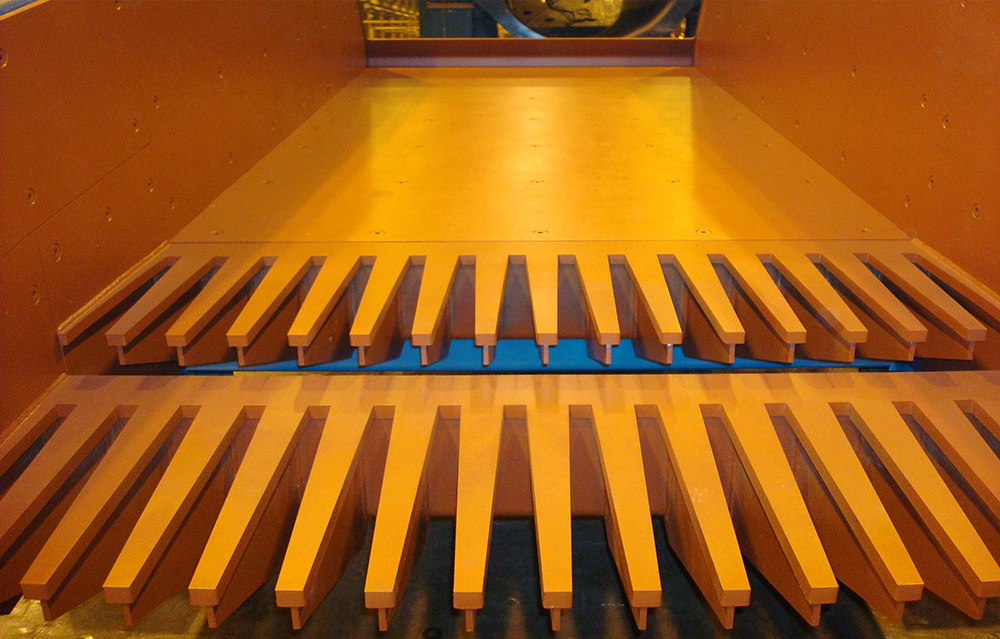
SECONDARY FINES SCREENS
General Kinematics’ High-Energy Secondary Screens in conjunction with GK’s FINGER-SCREEN™ Primary Screen for resource recycling has proven to be highly successful in a wide range of applications that are prone to process challenges common to other types of screening media.
GK’s Secondary Screens use vibratory action to separate fines from the secondary sort line material. The Two-Mass, low horsepower design has few moving parts for minimal maintenance and maximum uptime. Secondary Screens are heavy-duty with superior wear resistance and durability compared to rotary trommels or star-type screens.
The heart of your sorting system
Increased reliability, higher tonnage capacity and unsurpassed wear resistance make GK’s Secondary Screens the heart of sorting systems around the world. The superior performance of vibratory processing with GK’s unique FINGER-SCREEN™ deck delivers highly efficient separation and classification. The vibratory action spreads material across the deck thereby lowering the bed depth for maximum utilization of the screen area. Tapered finger designs along with unique cam-out surfaces and staggered positions help to prevent material bypass. Separation performance is further enhanced as material freely cascades down the deck with less plugging, trapping, or pegging. The result: continuous, dynamic material flow to enhance and optimize separation and classification.
GK’s Secondary Screen is available in standard sizes with widths up to 72 inches (1800mm) with custom sizes engineered based on your application. Capable of processing high volume production rates up to 450 yards per hour (345 cubic meters per hour).
Vibratory motion evenly spreads material for maximum classification efficiency.
Staggered fingers prevent material bypass.
Cascading material flow helps separate entrapped items.
Unique cam-out surface helps eliminate catching and binding.
Tapered fingers gradually classify and free tangled materials.
Custom-engineered to meet your specific classification requirements.
Modular deck construction permits easy deck replacement.
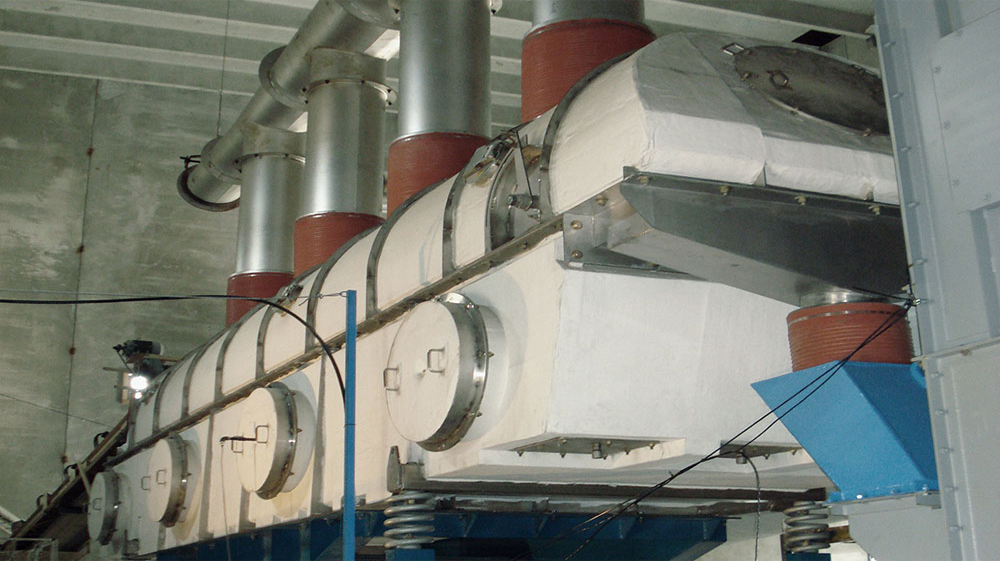
ASR DRYING SOLUTIONS
Do you wish your ASR were dryer? Current technologies are set up to maximize metals recovery in ASR, with the exception of the fines fraction where the majority of moisture is contained. Dry material is required in order to effectively recover metal from fines. General Kinematics’ Fluid Bed Dryer provides a cost-effective solution to help you recover the most from your ASR.
With an array of options available, GK’s Fluid Bed Dryer is a versatile part of your downstream ASR process operations. Capable of continuous or batch processing, each fluidized bed is custom engineered to meet your needs.
Contact a GK Recycling Technology expert for specific application solutions.
GK Vibratory Fluid Bed Dryers provide intimate contact with the materials for maximum drying effectiveness and increased metals recovery.
Available in virtually any dimension to maximize your process throughput.
Fluidized beds can cool, dry, and heat.
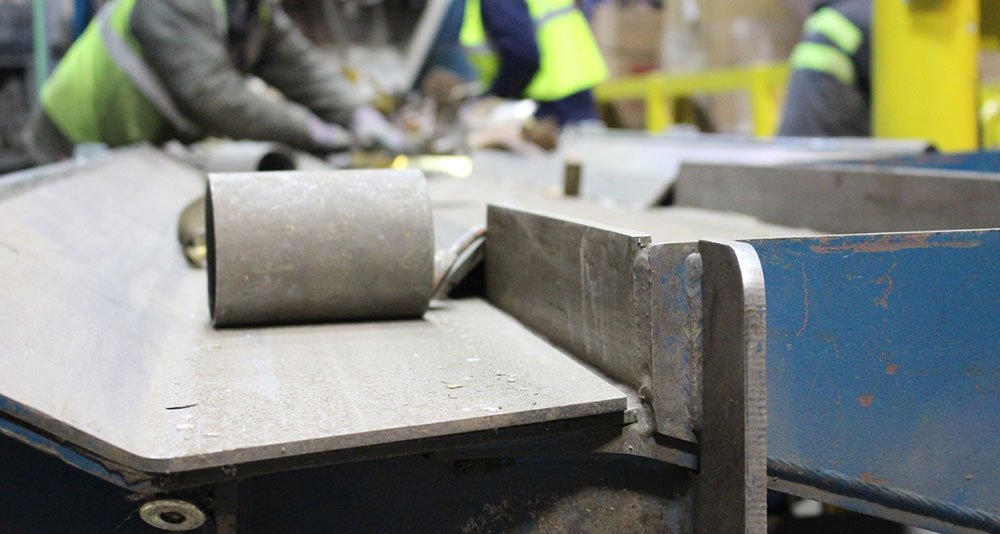
MIXED METAL SORTING SYSTEMS
General Kinematics Mixed Metal Sorting Systems incorporates a tote dumper and vibratory metering feeder working in conjunction with a sorting conveyor. GK’s patented Flat Stroke Sorting Conveyor, reduces worker fatigue associated with noise and vibration in common transfer conveyors. This sorting conveyor is specifically designed with minimal vertical stroke for quieter operation while still conveying into multiple lanes. Material is loaded into the hopper and evenly metered to the sorting conveyor where workers are able to utilize the conveyor lanes to organize material types. Systems such as this equate to a better working environment for employees and better recovery of mixed metals.
FEATURES:Custom designed to fit your current tote configurations.
Operator controlled metering feeder.
Multiple lane configurations available per application.
vGentle shuffle action of material for reduced worker fatigue.
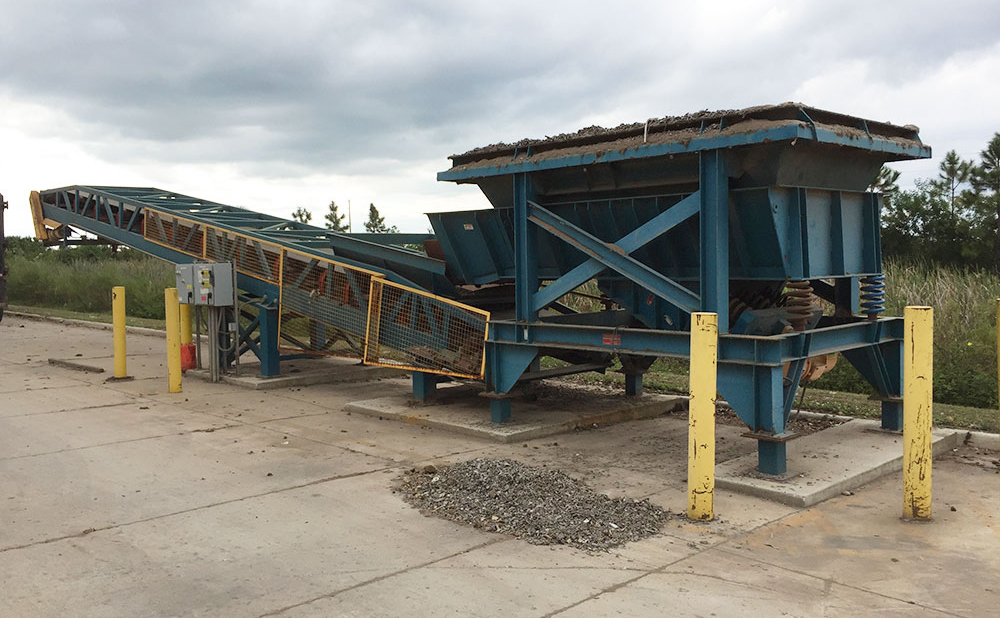
LOAD-RITE™ CONTAINER LOADING SYSTEMS
Minimization of empty container space is important to maximize your profitability of each container load. GK’s LOAD-RITE™ Container Loading System allows you to maximize the shipping weight of your container from back to front. Material is directly loaded onto GK’s heavy-duty PARA-MOUNT II® vibratory feeders, and is evenly distributed onto a belt conveyor which is inserted into your container. As the truck slowly pulls forward, the belt continuously feeds the container until it reaches the maximum volume.
GK offers systems based on your specific application:FERROUS SHRED:
20’ or 40’ Overseas Containers
Fill 45,000 lbs. in under 10 minutes
Vibratory Two-Mass Feeder to minimize bridging
Metered transition onto high speed belt conveyor
Optional belt scale for precise control
FEATURES:
Heavy-Duty feeder withstands heavy impact.
Custom hopper sized to suit bucket loader.
Low horsepower design reduces energy requirements.
Systems are available in fixed and skid mounted designs.
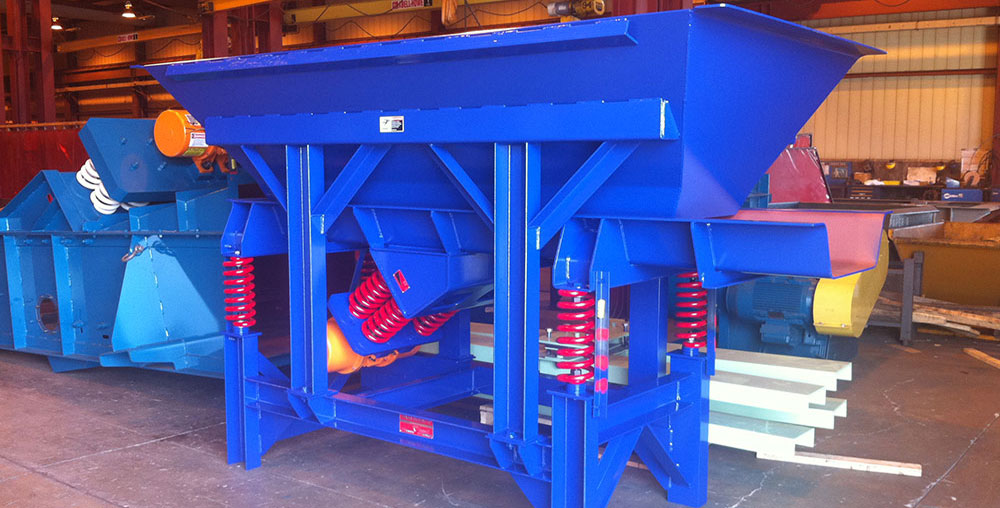
PARA-MOUNT II® VIBRATING FEEDERS
Proven performance and maintenance free operation make PARA-MOUNT II® Vibrating Feeders the first choice in vibratory feeders for the most demanding applications. PARA-MOUNT II® Vibrating Feeders in either fixed or Variable Force configurations utilize a sub-resonant Two-Mass system. Mass A (the exciter) energizes Mass B (the deck assembly) through precision engineered coil springs. Only small amounts of energy are needed to maintain the natural energy stored and released by the spring system. What this means for you is dynamic response to load surges, increased feed capacity, and exceptional reliability and ease of maintainability. PARA-MOUNT II® Vibrating Feeders are specifically designed to enhance your process.
FEATURES:Low maintenance, maximum uptime for reliable performance.
Simple, extra-heavy duty construction for years of trouble free service.
Two-Mass, sub-resonant natural frequency design is dynamically responsive to automatically maintain constant feed rate for varying load and material changes.
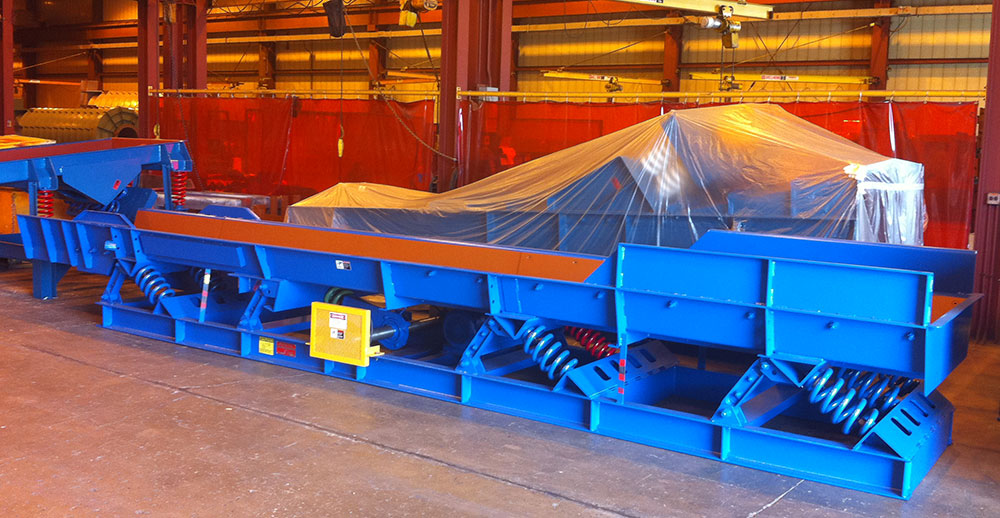
SHEAR TAKE-AWAY CONVEYORS
General Kinematics Shear Take-Away Conveyors are specifically designed to handle the severe conditions found underneath shears in scrap processing operations. Heavy-duty wear resistant troughs handle the impact of falling material while the exclusive General Kinematics SYNCRO-COIL® drive is designed to handle the force of even the largest impacts without damage to the conveyors drive system.
FEATURES:Heavy-Duty AR Liner – thick, replaceable, standard in the impact load area.
Down Stops – heavily reinforced load area with down stops to absorb the large material impacts.
Side Discharge – fines removal section with side discharge chute at the discharge.
Slave Trough – complete with down stops for maximum loading.
Motion Switch – sensor to warn of restricted movement.
Custom Sizes – to match existing units or for new installations.
Energy Efficient – natural frequency design minimizes power requirements.
Coil Spring Drive – that absorb momentary impact loading saving the drive bearings.
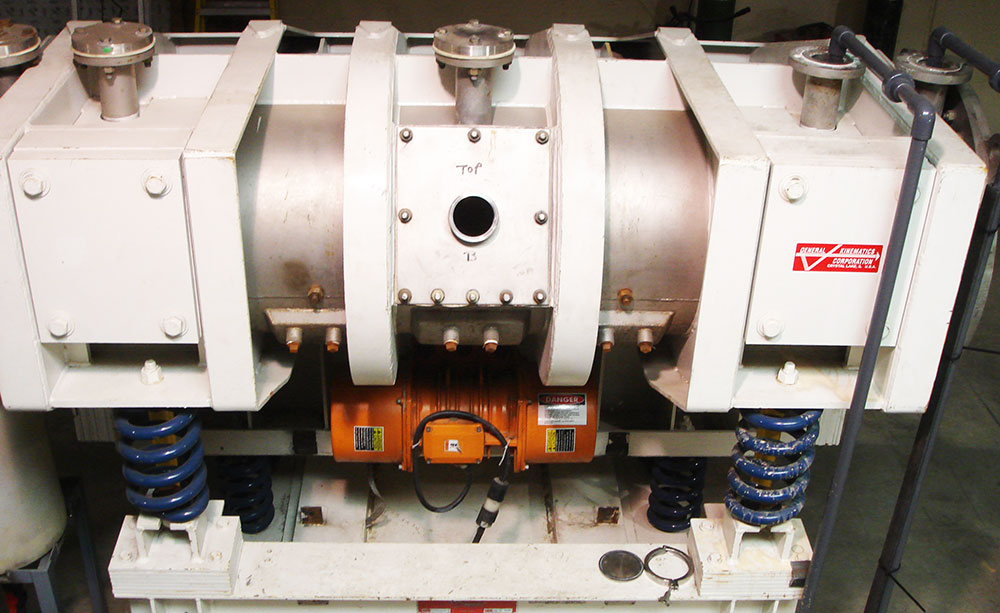
ASR VIBRA-DRUM® GRINDING MILLS
ASR VIBRA-DRUM® Grinding Mills are proven in dozens of milling applications and are the latest enhancement process for ASR recovery. The unique grinding action reduces the non-metallic minerals to enhance metals recovery.
Are you trying to recover additional precious metals like gold, silver and platinum from your ASR fines? Effective grinding performance and energy savings are the result of the VIBRA-DRUM® Grinding Mill’s natural frequency design. The sub-resonant, Two-Mass drive and spring system for minimal energy requirement and optimal performance are able to fracture rock, glass, and other materials into fine powder. This material can then be easily screened to achieve a concentrated metals stream. This also increases the efficiency of subsequent equipment by providing a better product.
Contact GK to find out if we can improve your grinding process.
Increased precious metals recovery from ASR fines stream.
Low energy requirements for efficient operation.
Can use any type of grinding media.
Non-rotating body allows for simple input and outlet connections.
Available in standard and custom sizes.