GRINDING AND ATTRITION
Internal and external changes to grinding equipment have increased efficiency and safety. The ability for units to extract minerals with less energy per revolution reduces overall cost of the machinery. GK vibratory grinding solutions are more compact, taking up less room and making them easier to install. The use of vibration, in combination with grinding media, significantly increases the number of material impacts per minute, decreasing extraction time and creating a more desirable fractured product. The ability to extract ore and minerals quicker allows units to process material more efficiently than older units, so retention time required to extract material is significantly reduced.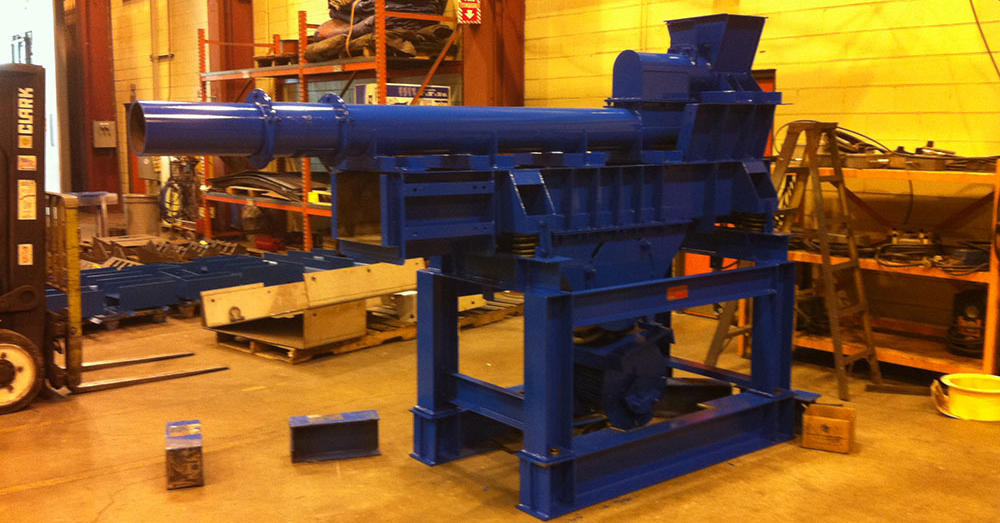
HMG™ VIBRATORY TUBE CRUSHER
General Kinematics patent pending HMG™ Vibratory Tube Crusher quickly breaks down material. Rapid pulsation of media within the tube fractures material into smaller particles ideal for final comminution in GK’s VIBRA-MILL® Grinding Drum.
FEATURES:Can be totally sealed for a dust free environment.
Low horsepower drive reduces energy consumption and electrical costs.
Available in custom sizes to best fit your throughput and application.
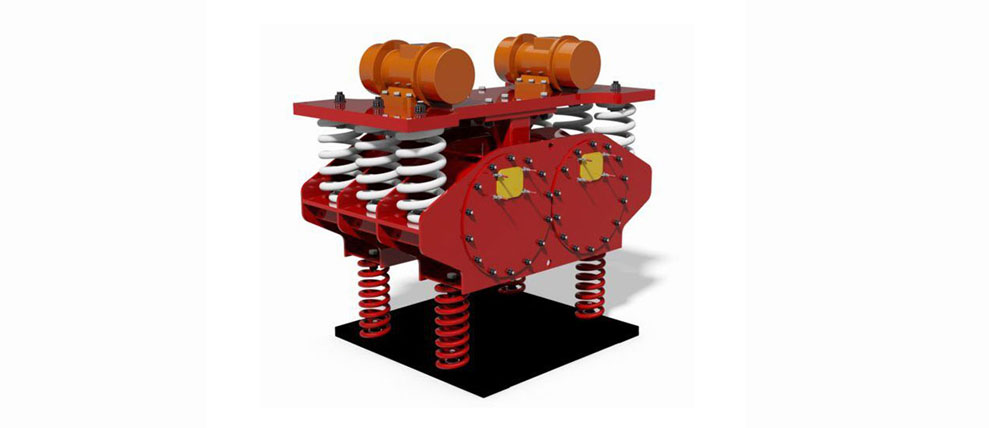
VIBRA-DRUM® DOUBLE BARREL GRINDING DRUM
The GK VIBRA-DRUM® Double Barrel Grinding Drum is an energy-efficient, vibratory drum capable of breaking down materials more effectively. This innovative design is capable of processing more material for less capital cost and in a tighter footprint than standard single barrel grinding drums.
With a proportionally higher spring rate for higher energy, the Double Barrel Grinding Drum provides better control over the material flow.
In addition, the VIBRA-DRUM® Double Barrel Grinding Drum is backed by GK technical support. Ask our experts!
FEATURES:
Higher Energy
Faster Grind
Simple Design
Cost Effective
Smaller Footprint
PRODUCT QUALIFICATION:
The VIBRA-DRUM® is proven to efficiently grind:Alumina | Aluminum Oxide | Barite | Barium Ferrite | Calcined Magnesite | Cement | Clay | E-Scrap | Ferro-Silicon | Gerro Alloys |
Graphite & Synthetics | Iron Oxides | Magnetite | Mechano-Chemical Grinding | Metallic Slag | Moly | Nickel/Ferro Chrome Alloys | Various Ores – Copper, Iron, Gold | Chrome Carbide | Petroleum Coke |
Phosphate | Precious Metals | Quartzite | Shale | Silica Sand | Silicon Carbide | Silicon Metal | Slags, various | Titanium | Tungsten Carbide |
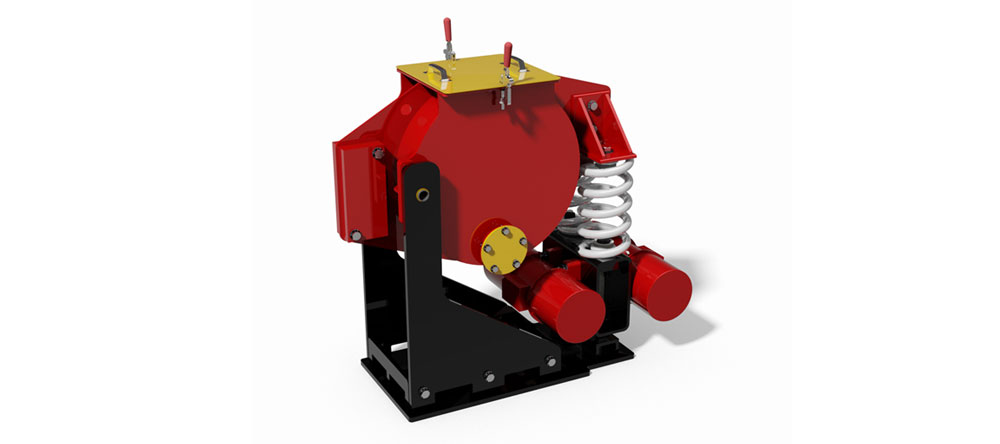
VIBRA-DRUM® LAB SCALE GRINDING DRUMS
The GK VIBRA-DRUM® Lab Scale Grinding Drum is an energy-efficient, vibratory drum capable of breaking down materials more effectively. The unique attrition capabilities of the VIBRA-DRUM® make it ideal for offline testing scenarios to keep your production flowing.
Ideal for occasional batch grinding use, the VIBRA-DRUM® Lab Scale Grinding Drum is backed by GK technical support. Ask our experts!
VIBRA-DRUM® Lab Scale Grinding Drum is versatile and easy to use.
Fine grinding: 3000 microns – 5 microns.
Allows your facility the opportunity for on-site project testing which can help ensure representative product and process.
Economics make it reasonable for use in cases where customers need to process occasional batch grinding.
Chamber material fabrication means it is suitable for many chemical processes such as grinding during initial leach of precious metal recovery operations.
Lab data from drum can directly be used for scaling up.
Easy to move via forklift.
Less than 1200 lbs. and no special foundations required.
PRODUCT QUALIFICATION:
The VIBRA-DRUM® is proven to efficiently grind:Alumina | Aluminum Oxide | Barite | Barium Ferrite | Calcined Magnesite | Cement | Clay | E-Scrap | Ferro-Silicon | Gerro Alloys |
Graphite & Synthetics | Iron Oxides | Magnetite | Mechano-Chemical Grinding | Metallic Slag | Moly | Nickel/Ferro Chrome Alloys | Various Ores – Copper, Iron, Gold | Chrome Carbide | Petroleum Coke |
Phosphate | Precious Metals | Quartzite | Shale | Silica Sand | Silicon Carbide | Silicon Metal | Slags, various | Titanium | Tungsten Carbide |
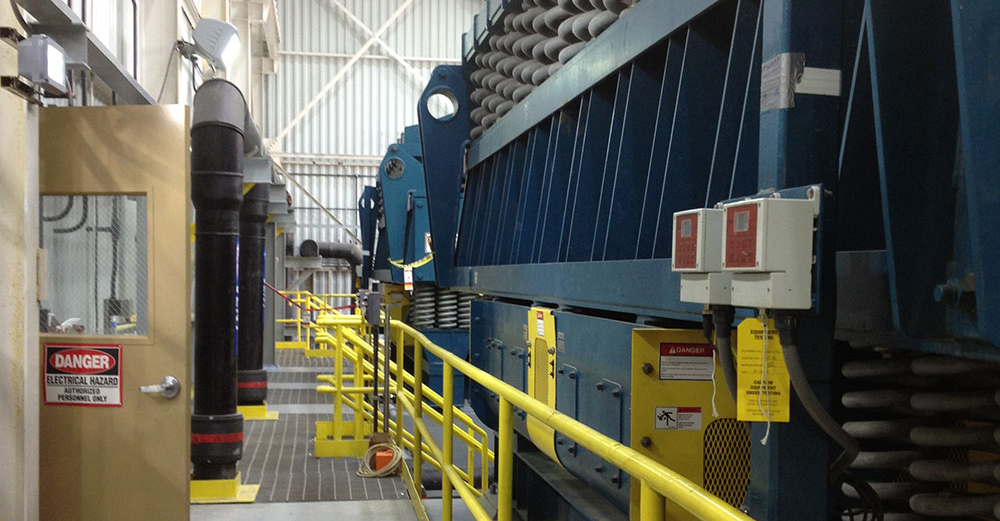
VIBRA-DRUM® GRINDING MILL & SOLUTIONS
MAXIMIZE MATERIAL RECOVERY WITH GK’S VIBRA-DRUM® TECHNOLOGY FOR GRINDING, CRUSHING AND LEACHING!
General Kinematics VIBRA-DRUM® Grinding Mills are proven in dozens of milling applications in the mining and mineral industries.Each grinding mill is achieving impressive energy savings (35-50%), thanks to a unique rotational material motion that is more efficient than conventional ball or rotary grinding mills. New processes such as micron grinding and mechanochemical grinding give our customers a unique and effective competitive advantage.
VIBRA-DRUM® Grinding Mill units are also ideal for continuous processing of “difficult-to-fluidize” products such as large flake and stringy or tacky materials. Typical VIBRA-DRUM® Grinding Mill applications include direct gas contact heating, drying, cooling, and coating.
Need more information about the General Kinematics VIBRA-DRUM® Grinding Mills? Ask our experts!
HOW IT WORKS:
Exceptional grinding performance and energy savings are the result of the VIBRA-DRUM® natural frequency design. A sub-resonant, two mass drive and spring system alternately stores and releases grinding power. Once in motion, energy is only needed to move the grinding media as a fluid mass, and to overcome frictional losses.The increased number of impacts in the VIBRA-DRUM® Grinding Mill results in a faster, more efficient grinding action. As the grinding mill vibrates, media particle migration is experienced in both axial and transverse directions. In fact, the media migrates through the VIBRA-DRUM® Grinding Mill in a path similar to that of a rotary grinding mill without lifters, but each media particle imparts positive impact energy at each vibration.
The area where comminution takes place is larger and more efficient compared to a rotary grinding mill of similar size. There are no dead zones of inactive media inside the vibrating grinding mill. And, unlike stirred or tower grinding mills which grind by attrition, the VIBRA-DRUM® Grinding Mill uses the principle of impact grinding which causes clean breaking and does not coat the mineral/gangue with slimes.
The VIBRA-DRUM® Grinding Mill can be used for processes other than grinding. It has been used to:
process and agglomerate fiberglass
mix product components
clean castings
for hydrometallurgy
minerals recovery
and other processes.
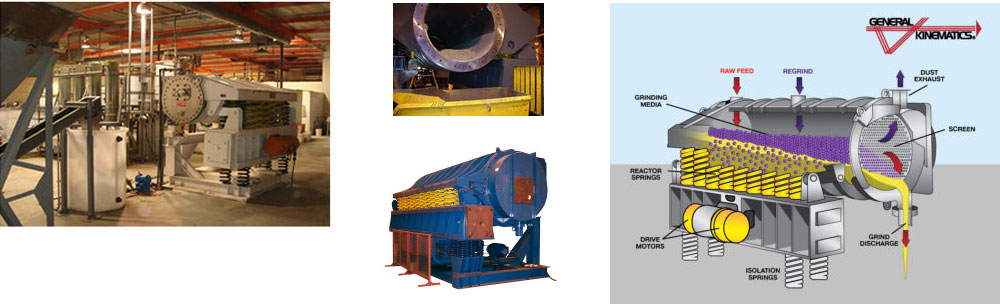
MINIMAL INSTALLATION COSTS:
The capital cost of a VIBRA-DRUM® Grinding Mill is significantly less than a rotary grinding mill containing a comparable media load. There are no drive speed reducers, ancillary machinery, nor large support bearings. The VIBRA-DRUM® Grinding Mill has very few moving parts.A VIBRA-DRUM® Grinding Mill does not require the typical massive concrete foundation required of a conventional rotary grinding mill unit. Structural steel supports are designed as an integral part of the VIBRA-DRUM® Grinding Mill and simply bolted to a suitable load-bearing floor.
The grinding chamber in the VIBRA-DRUM® Grinding Mill requires replaceable liners on only 60% of its circumference, representing a considerable saving in initial installation and mill downtime. Theoretically the VIBRA-DRUM® need not be a tube shape, however, this shape was chosen because of its shell strength.
Contrary to rotating devices the VIBRA-DRUM® Grinding Mill offers the advantage of relatively static access to the mill while it is operating. The controlled addition and even distribution of chemicals, the sampling of material in progress, or the discharge of product at any point in the mill offers endless possibilities.
LEACHING APPLICATIONS:
The VIBRA-DRUM® in a wet grind leaching application provides efficient chemo-mechanical processing of ore bodies for precious metal recovery.MAINTENANCE:
Minimal moving parts and innovative engineering combine to provide you with a grinding mill that requires little maintenance and downtime requirements.The maintenance of the VIBRA-DRUM® products consists of…
Periodic lubrication of motors.Easy liner replacement system uses clamp bars for quick replacement.
Access doors allow easy inspection of media and liner.
Media changes simplified by removal of endcap bolts
FEATURES:
Proven energy savings range from 35 to 50% reductions in kW hours per ton of processed material.
5 to 10 times longer media life.
No trunnions, wheels, gears or drive reducers.
Few moving parts assures low maintenance.
Adjustable media action, from gentle to aggressive.
One half the liner requirements of typical rotating designs.
Easily installed. Low dynamic reaction force eliminates massive foundation requirements.
Recoveries of 93 – 97% can be achieved without the use of toxic chemicals such as arsenic due to the unique fracturing in the ore from General Kinematics Mill as well as our leaching solution.
Liberation of precious metals due to the non-compression nature of milling.
Fracture of ore saturated in zones of microcrystalline areas.
Heavy pulp density for maximum ore processed per gallon of liquid.
System is fully automated.
In-situ leaching eliminates external leaching componentry and helps control chemistry.
PRODUCT QUALIFICATION:
The capabilities of the VIBRA-DRUM® Grinding Mill are unmatched. Extensive in-house or on-site testing is available to qualify your product requirements. General Kinematics also offers wet or dry particle analysis as well as access to our on staff material scientist for further material qualification.The VIBRA-DRUM® Grinding Mill is proven to efficiently grind:
Alumina | Aluminum Oxide | Barite | Barium Ferrite | Calcined Magnesite | Cement | Clay | E-Scrap | Ferro-Silicon | Gerro Alloys |
Graphite & Synthetics | Iron Oxides | Magnetite | Mechano-Chemical Grinding | Metallic Slag | Moly | Nickel/Ferro Chrome Alloys | Various Ores – Copper, Iron, Gold | Chrome Carbide | Petroleum Coke |
Phosphate | Precious Metals | Quartzite | Shale | Silica Sand | Silicon Carbide | Silicon Metal | Slags, various | Titanium | Tungsten Carbide |
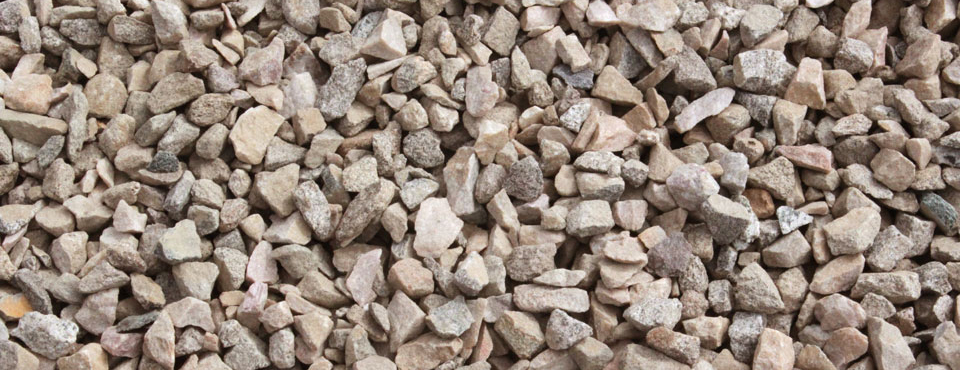
VIBRA-JAW™ VIBRATORY JAW CRUSHERS
General Kinematics VIBRA-JAW™ Vibratory Jaw Crusher uses high energy vibration to rapidly reduce materials into smaller particle sizes. Vertical impact surface is easily adjustable to fine tune throughput size, and self relieving impact plate reduces jam-ups and downtime. Utilizing GK’s Two-Mass Technology, units use very minimal energy, reducing your electric consumption and utility expenses.
FEATURES:VIBRA-JAW™ is easy to service, with few moving parts.
Two-Mass drive is energy efficient and easy to maintain.
Impact area is easy to adjust, and high wear impact plates are easy to replace.
Custom engineered to your material and throughput requirements.