LOST FOAM CASTING SYSTEM
From sand conditioning to mold compaction in a single, automated process.
General Kinematics combines design innovation, process know-how, and vibratory technology into a precision, versatile compaction system engineered for quality results plus cost efficient operation.Vertically stacked vibrating components conserve floor area and provide continuous free flow of sand through each processing stage. GK’s lost foam system delivers immediate user benefits:
From development to production
GK lost foam casting systems allow process development to determine optimum procedures… then can be programmed to operate as a high volume production system… all with the same equipment.Compact, cost efficient
Using a minimum of floor space, GK lost foam casting systems require no pits or special foundations. Low energy motor driven components operate with minimum cost and maintenance.Sealed process
Dust collection is required at the flask fill station only, with all other stages linked by flexible seals.Adaptable to your needs
GK lost foam systems can be adapted to any size flask used in your operation.Low maintenance, quiet design
All components utilize reliable, sealed, motorized drives to assure acceptable sound levels. Absence of other moving parts minimizes maintenance requirements.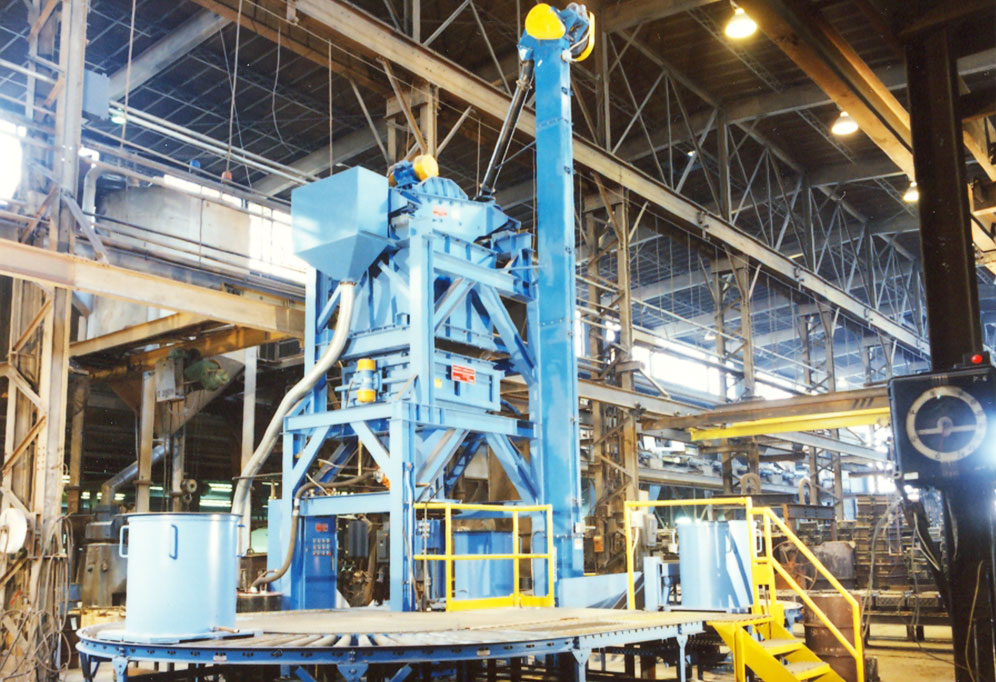
FEATURES:
Screener – Sand is introduced through the General Kinematics vibrating screener / classifier unit mounted at top of equipment stack. Unit maintains desired grain size distribution and removes undesirable fines.
Shut-off Gate – Sand flows into surge hopper equipped with a pneumatically operated bottom gate which permits system shut-down without unloading.
Cooler – The General Kinematics VIBRA-FIN™ sand cooler senses inlet temperature and automatically cools sand to ideal molding temperature.
Distribution – Sand flows through second hopper into a flow control and distribution unit which uniformly rains sand into flask. Gentle rain pattern eliminates distortion of fragile patterns. Specific areas can be masked if desired.
Compaction – General Kinematics compaction table is isolated on a pneumatically operated lift frame which is raised to precisely position flask at fill station. Following automatically sequenced compaction cycle, table is lowered allowing filled flask to be transferred by roller conveyor or automated flask handling system.
Gripper – Pattern is initially positioned and held within flask by pneumatically operated gripper which relaxes its grip as compaction cycle progresses.