SAND PROCESSING AND HANDLING
General Kinematics Vibratory and Rotary equipment are unequaled in efficiency and performance in a foundry application. Each of GK’s proven designs are specially designed for screening, conveying, cooling or drying of foundry sand.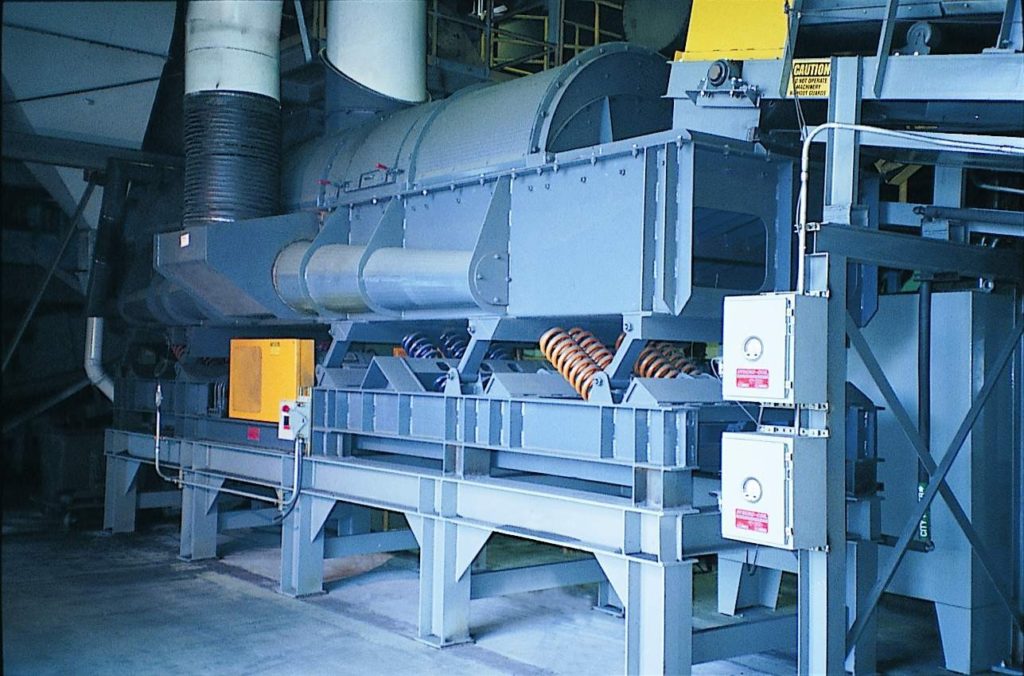
VIBRATORY FLUID BED SAND COOLERS
General Kinematics Vibratory Fluid Bed Sand Coolers are specially designed for evaporative cooling or drying of foundry sand. Air distribution decks are engineered to provide complete control of airflow for exceptional drying or cooling efficiency.
FEATURES:Choice of vibratory balancing styles or isolated designs to suit specific installation requirements for foundations or structures.
Custom designed to meet your sand cooling throughput needs to 500 tons or greater.
Infinitely adjustable controls provide variable retention time and improved process efficiency.
Inlet air distribution manifolds minimize costly stationary ductwork and supports.
High efficiency, low horsepower Two-Mass drive reduces energy requirements.
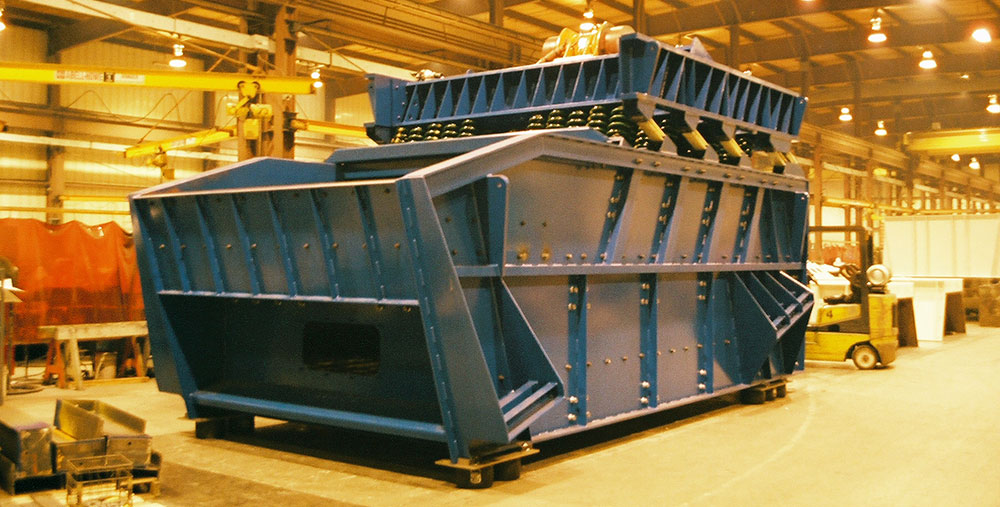
VIBRATORY FOUNDRY SCREENS
General Kinematics Vibratory Foundry Screens are unequaled in efficiency and performance in a foundry application. GK’s proven two-mass drive system reduces electrical consumption and increases screening efficiency over traditional direct drive (brute force) designs. Options include replaceable decks, multiple decked units, banana style decks, and special corrosion resistant finishes. GK Vibratory Foundry Screens are available in standard and custom sizes to easily fit into existing processes.
FEATURES:Two-mass design achieves up to 5 times electrical savings over typical direct drive screens (150 HP compared to GK’s 30 HP).
GK Two-Mass Screens are load responsive. The higher the tonnages, the higher the screening efficiencies.
Two-mass design maintains stroke level, while brute force loses stroke as more material is added.
The GK Two-Mass screen is “plug and play.” Simply plug it in and you are up and running.
Compact, low HP vibratory motors are mounted to the unit for fast change-outs.
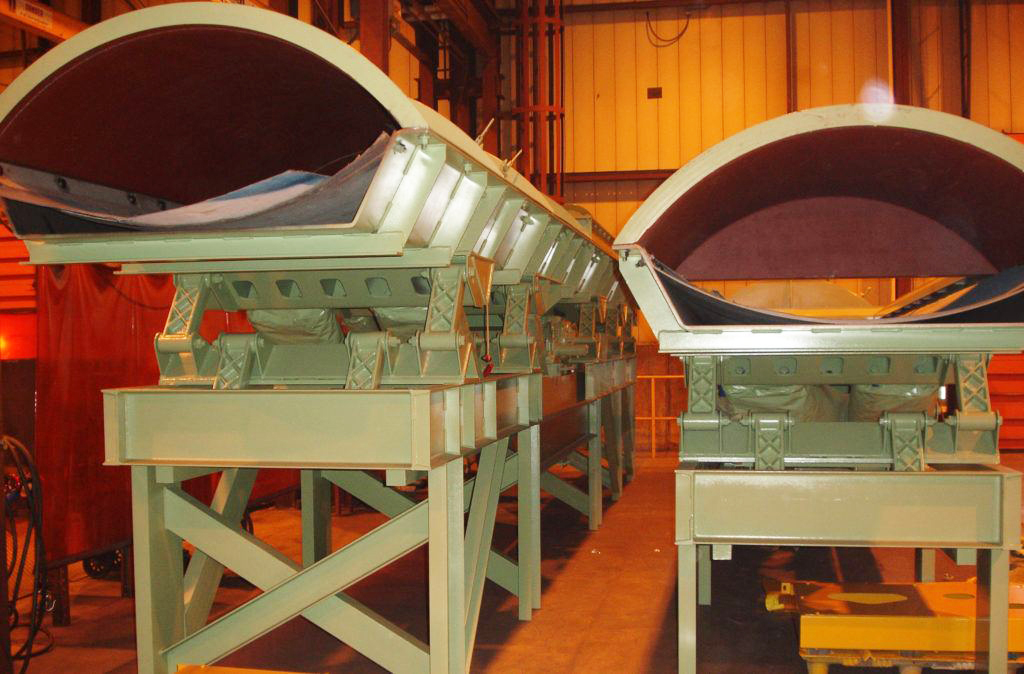
VIBRA-BELT® VIBRATORY BELT CONVEYOR
VIBRA-BELT® Vibratory Belt Conveyors combine the best features of vibrating conveyors and belt conveyors into one superior material handling concept.
The VIBRA-BELT® Vibratory Belt Conveyor has a flexible trough suspended between the sides of a trough provided with General Kinematics proven vibrating conveyor drive and reactor system components. The result is an improved belt conveyor system, adaptable to a variety of materials and operating conditions, incorporating the incomparable reliability and cleanliness of vibratory equipment.
Flexible conveying surface can be fabricated of various materials, including stainless steel, to successfully handle hot, sticky, fragile, or other “difficult to handle” materials. VIBRA-BELT® units are available in lengths up to 300 feet and in variable widths, depending on your application.
Ideal for materials that tend to stick to a metallic trough surface since a vibrating motion causes the suspended trough to flex, preventing material build-up.
Low profile, compact design fits where other conveyors cannot be installed.
No belt tracking problems or conveyor idlers to lubricate and maintain. Only a single vibratory conveyor eccentric drive requires periodic lubrication.
Material conveying speeds can be fixed or adjustable rate.
Dust tight and ventilated construction available.
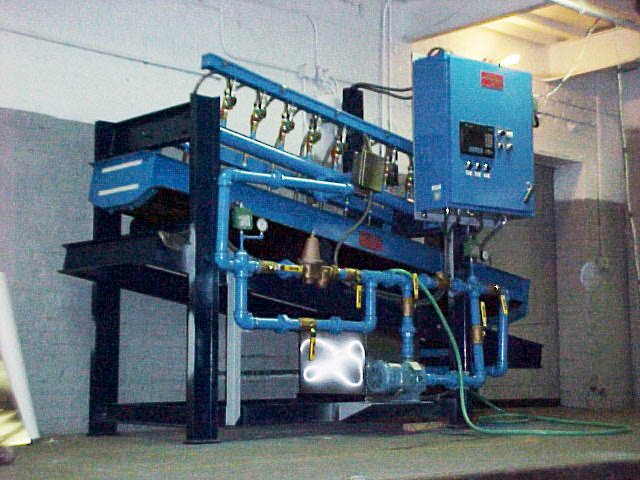
SPRAY-COOL™ WATER ADDITION SYSTEMS
General Kinematics SPRAY-COOL™ water addition systems provide precise in-process sand conditioning and cooling of foundry sand. SPRAY-COOL™ improves the efficiency of fluid bed sand coolers and systems based on evaporative cooling. Combining in-process temperature and weigh sensing components and water spray nozzles, SPRAY-COOL™ systems deliver the exact amount of water needed to achieve a pre-set moisture/temperature for sand conditioning, regardless of changing flow rates and varying sand temperature.
FEATURES:Precise control of water flow based on material moisture.
Adaptable to existing equipment or can be a stand alone process.
Ideal for cooling sand and castings.
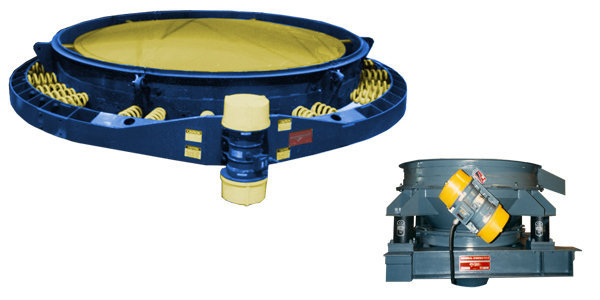
HULA-HOPPER® BIN ACTIVATOR / FEEDER
The General Kinematics HULA-HOPPER® Bin Activator is an improved vibratory equipment concept based on operating principles proven in thousands of General Kinematics installations. Within a single, extremely low headroom unit, the HULA-HOPPER® combines material activation, infinitely variable flow rate control, and positive flow shut-off all into one bin activator unit; yet installation, service, and operating costs are dramatically lower than for comparable bin activator systems.
HULA-HOPPER® Bin Activator eliminates many problems associated with more complex, brute force vibratory machinery because of its simplified operating design. As a Two-Mass vibratory unit, the HULA-HOPPER® Bin Activator uses a low-horsepower motor drive, therefore electric power needs are minimal. Orbital action eliminates compacting and bridging because only material drawn out is activated.
Infinitely adjustable flow control using GK’s VF wheels or electronic VFD.
Extremely low headroom design reduces bin activator height requirements.
Easy to service design.
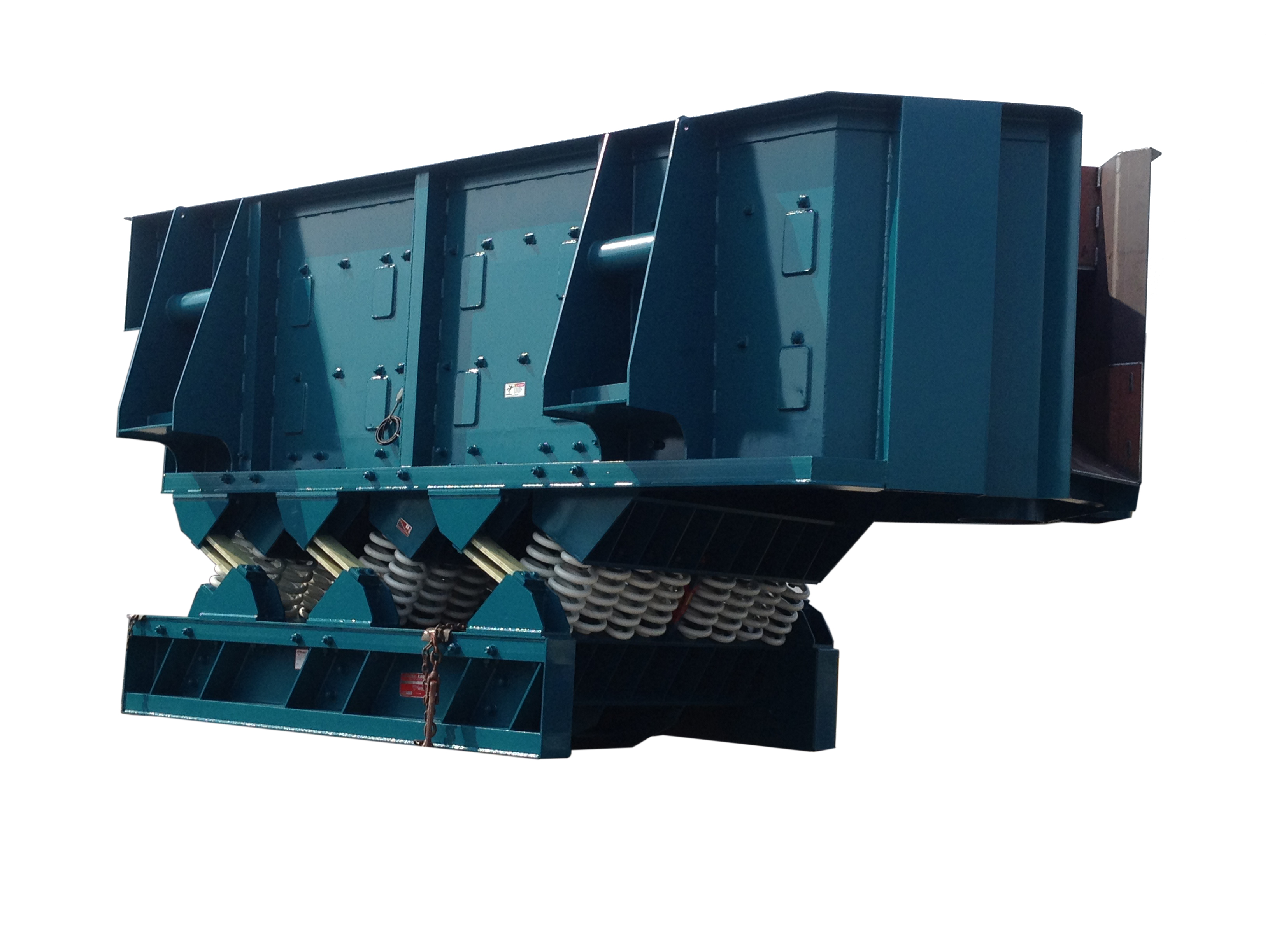
PARA-MOUNT II® VIBRATING FEEDERS
Proven performance and maintenance-free operation make PARA-MOUNT II® Vibrating Feeders the first choice in vibrating feeders for the most demanding applications. PARA-MOUNT II® Vibrating Feeders in either fixed or Variable Force configurations utilize a sub-resonant two-mass system. Mass A (the exciter) energizes mass B (the deck assembly) through precision engineered coil springs. Only small amounts of energy are needed to maintain the natural energy stored and released by the spring system. What this means for you is increased feed capacity, lower energy costs, and exceptional reliability and ease of maintainability. PARA-MOUNT II® Vibratory Feeders do more work with less energy, thanks to our two-mass, natural frequency design. Whether you are charging a feeder or metering sand or castings, each feeder is designed specifically to work to enhance your process.
FEATURES:Two-mass vibratory drive can be designed with low horsepower foot mounted or double c flange motors.
Simple, extra-heavy duty construction for years of trouble-free service.
Two-mass, sub-resonant natural frequency design is self-compensating to automatically maintain constant feed rate for varying load and material changes.
Significant annual energy savings over brute or direct force designs.
Engineered to be low maintenance for continuous uptime.
Extra-Heavy duty design withstands heavy parts and abrasive materials.
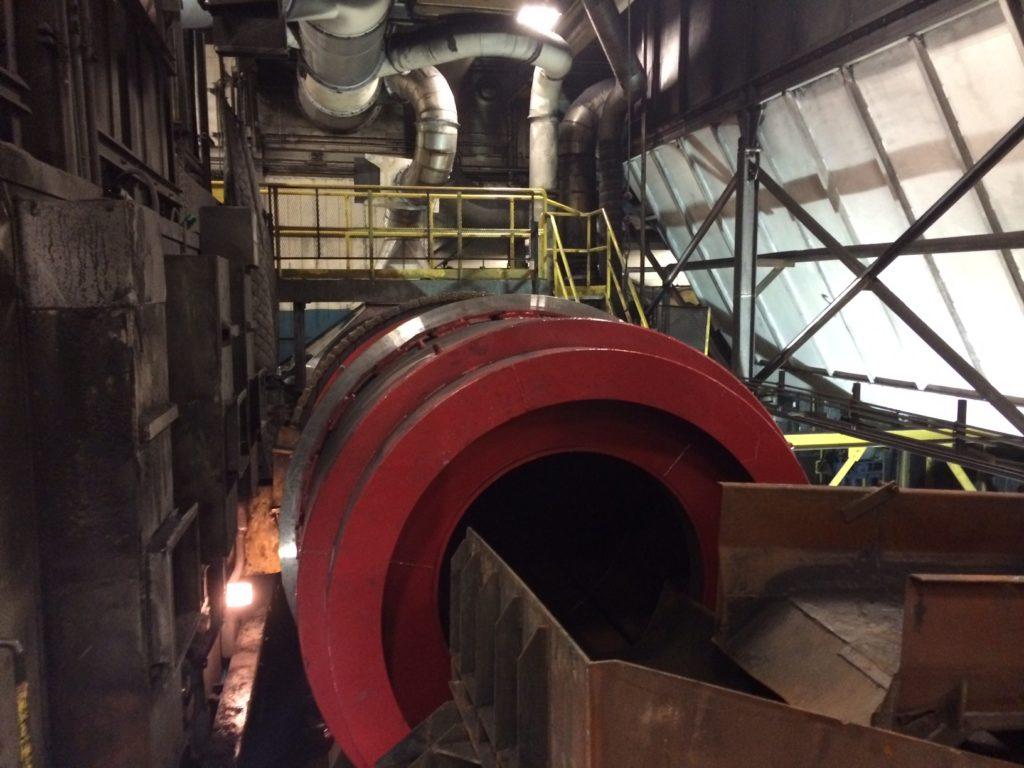
ROTARY SAND SCREEN
General Kinematics DUCTA-SCREEN™ Rotary Sand Screen blends and conditions sand, all while removing tramp metal and core butts for a cleaner sand recycle back to your sand system. Sand is broken down, leaves the rotary shell, and is deposited on GK’s vibratory sand take-away conveyor. The removal of sand from the rotary shell allows cooler equipment temperatures, allowing for increased equipment and component life.
FEATURES:GK fabricated liners are easier and safer to replace, and cost up to 75% less than cast grid systems.
Drum shell is not a wear item, saving you considerable maintenance funds and headaches.
Drums use easy to source commercially available components.
Available in standard and custom sizes to match your process design and throughput.