VIBRATORY & ROTARY SHAKEOUTS
In the modern foundry, there are many options when it comes to choosing the proper shakeout technology for your metal casting facility. General Kinematics is the only foundry equipment supplier which offers every type of vibratory and rotary shakeout solution. Not only that, GK also has proprietary, custom solutions that nobody else can make or offer you. This means that when a GK Foundry specialist recommends a piece of shakeout equipment, it is based on what is best for your application, not what is in our product catalog.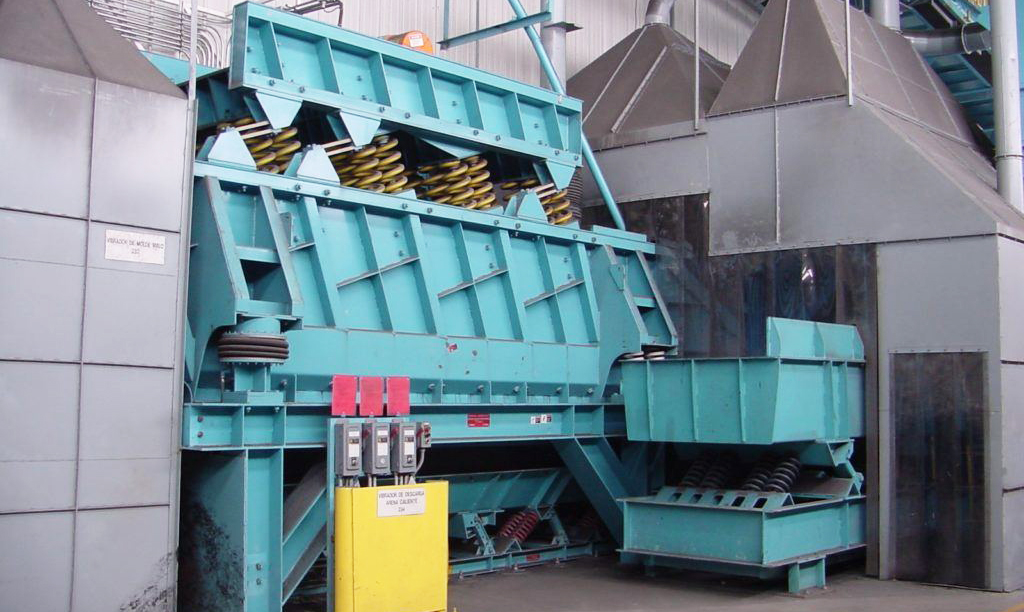
TWO-MASS CONVEYING SHAKEOUT FEEDER
General Kinematics’ high frequency, two-mass shakeouts will boost your foundry throughput. Our unique two-mass design automatically compensates for varying load conditions, assuring non-dampening shakeout performance.
General Kinematics shakeout feeders are specifically designed for your high production molding lines. Capacities range from 30 to 300 tons per hour for gray, ductile or malleable iron. Each shakeout feeder is sized to maintain the proper casting retention time to break down your sand while preventing excessive casting batter.
Two-Mass technology allows the use of variable frequency drives to vary the amount of g-force applied to break down the sand. General Kinematics’ specially designed isolation system allows for incline or decline of the shakeout surface thereby maintaining castings in the shakeout for the desired retention time based on your part number.
The unique GK two-mass design automatically compensates for varying load conditions, assuring non-dampening shakeout performance.
Driven with proprietary sealed vibration shaker motors, GK’s Two-Mass Shakeouts eliminate the need for V-belts, pivoted motor bases, couplings, and large and expensive bearings.
The drive for our shakeout feeders is mounted on a separate exciter mass, completely isolated from the high-intensity impact action of the shakeout deck.
Our vibration shaker units feature low horsepower, adjustable amplitude control, and exceptionally quiet operation.
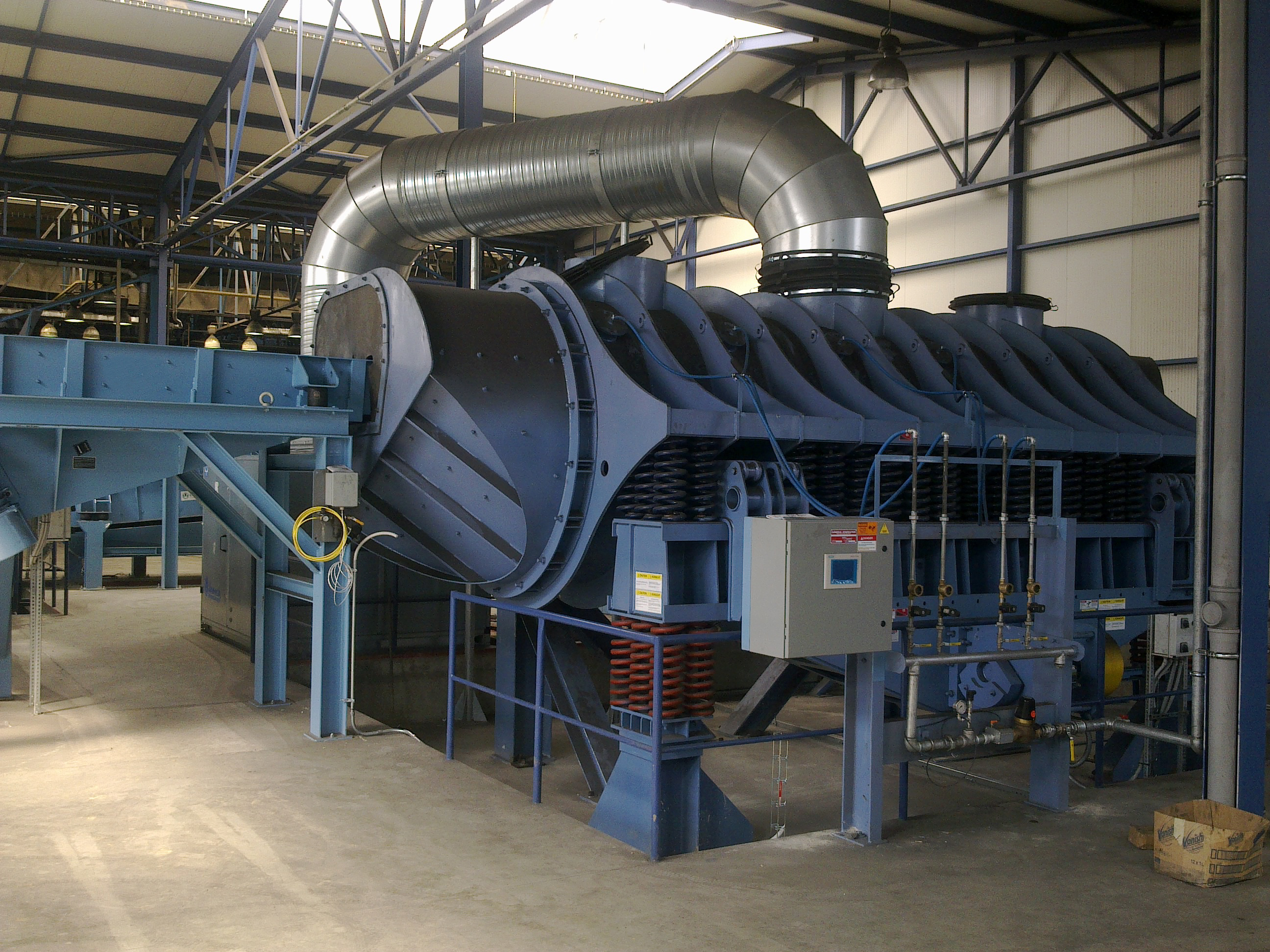
VIBRA-DRUM® SAND CASTING EQUIPMENT
Proven in hundreds of applications worldwide, VIBRA-DRUM® Sand & Casting Conditioners have revolutionized high volume mold/sand handling for foundry applications. This versatile Two-Mass system gently tumbles castings and provides accelerated casting cooling through equalizing of sand/casting temperatures and evaporation of moisture. This tumbling action reduces sand lumps to original grain size and blends sand to equalize shakeout sand temperature — all in one continuous, energy-efficient operation.
The gentle tumbling action of the VIBRA-DRUM® keeps the castings in a bed of sand, never dropping or creating impact during the shakeout process. This action provides the gentlest shakeout in the industry, allowing the automated shakeout of fragile castings.
The Two-Mass VIBRA-DRUM® delivers continuous shakeout operation, plus superior material motion for efficient sand and casting processing. Natural frequency vibration produces a beneficial drum-like material rotation that quickly reduces sand lumps without casting damage. High-frequency agitation efficiently reduces sand to original grain size. Put it all together and you have a simple, easy-to-maintain, non-rotating design with all the environmental benefits of a totally enclosed drum — but with no air handling, sealing, or interface problems and no casting damage.
Totally enclosed structure contains airborne silica and dust for a cleaner work environment.
The VIBRA-DRUM® brings controlled metallurgical cooling to castings for a better quality end product.
Non-rotation design is easier to feed, unload, hook up to your air handling system, and to maintain than competitive shakeout technologies.
The scrubbing action of the VIBRA-DRUM® produces cleaner casting surfaces, reducing shot blast consumable consumption up to 20%.
The two-mass drive system uses up to 2/3rd’s less energy compared to direct drive machines, creating substantial energy savings.
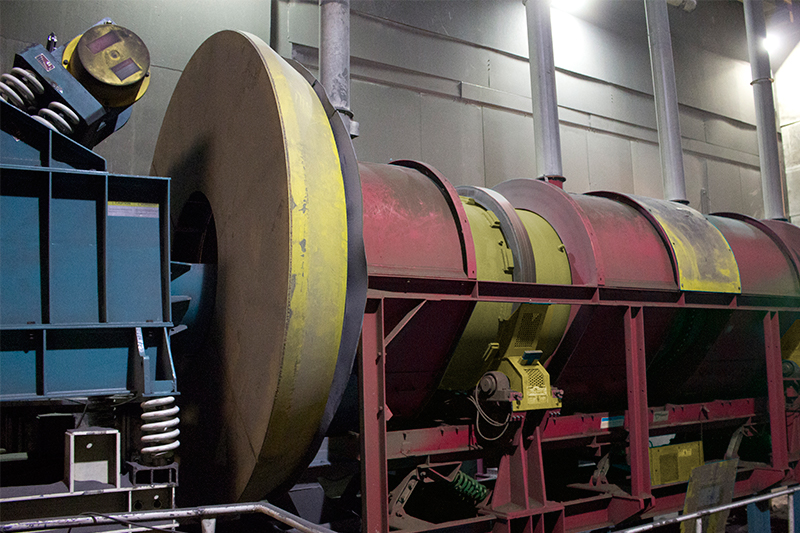
DUCTA-CLEAN® ROTARY MEDIA DRUM
Cleaner Castings and reduced maintenance are just two of the advantages the patent pending DUCTA-CLEAN® Rotary Media Drum can offer. Media scrubs castings, removing sand, all while separating sprue and gates from castings. Media, tramp metal, and sand then exit the drum onto a GK vibratory sorting conveyor, which completely screens sand from the media, separates tramp metal, and then returns media back into the drum via the GK ROTOVEYOR™ rotary return conveyor.
FEATURES:
Separation of sand, media, and tramp metal is done outside the rotating assembly on a GK vibratory processor, eliminating rotating mass and wear to the drum body.
GK fabricated liners are easier and safer to replace, and cost up to 75% less than cast grid systems.
Patent-pending liner system eliminates compression rings, heavy cast liners, and excessive maintenance costs.
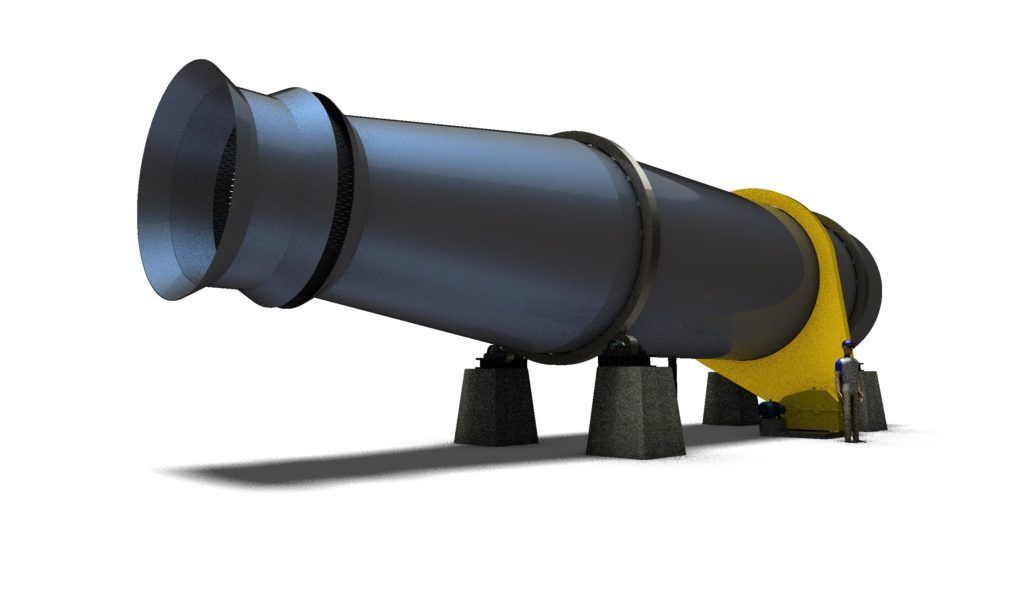
DUCTA-COOL™ ROTARY DRYERS AND COOLING DRUMS
GK’s DUCTA-COOL™ Rotary Drum combines sand cooling, sand and casting separation, and casting cooling in one efficient rotary drum. Gentle tumbling action, combined with air circulation, creates an evaporative cooling effect to reduce casting temperatures during processing. Sand lumps are broken down as well as blended prior to being screened off at the end of the drum, and is then returned to the sand system. Put it all together, you get one rotary dryer machine for multiple functions in an easy to install and maintain equipment package.
FEATURES:Sand cooling, sand and casting separation, and casting cooling in one efficient rotary drum.
Rotary dryers and drums are available in standard and custom sizes to match your process design and throughput.
Heavy-Duty construction ensures trouble-free operation for maximum uptime reliability.
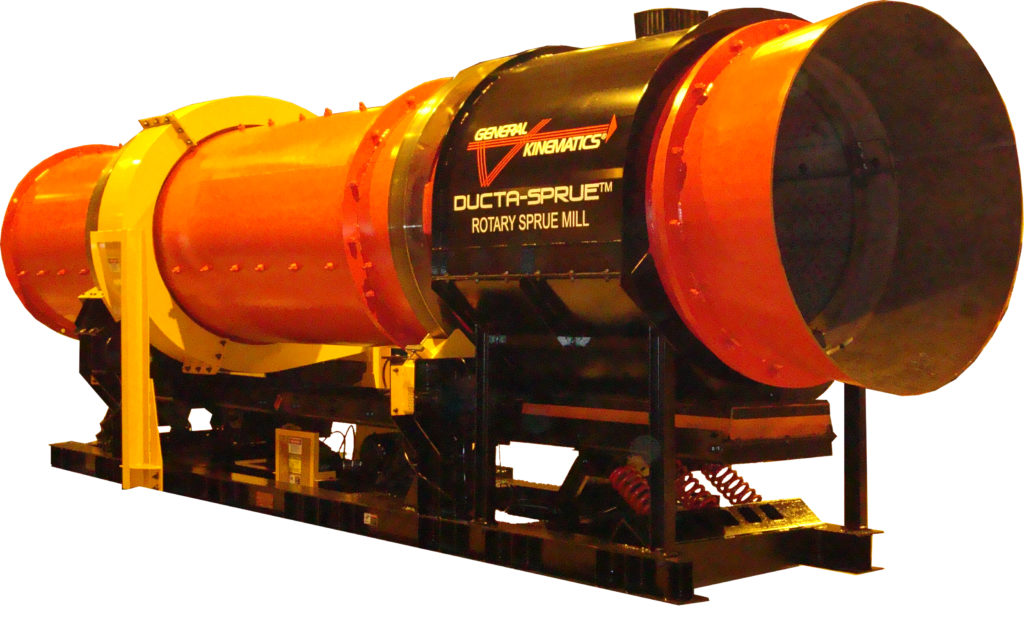
DUCTA-SPRUE® ROTARY SPRUE DRUM
The DUCTA-SPRUE® Rotary Sprue Drum combines innovative patented rotary technology with GK’s proven vibratory material transfer equipment to give you a long lasting, easy to maintain solution for processing sprue, gates, and core butts.
Users report that the direct savings resulting from the cleaning of gates, risers. runners, flash, fins, run-outs and other sprue, before charging them into a melting furnace has repaid the cost of the General Kinematic DUCTA-SPRUE® sprue mill and all accessory feeding and handling equipment in under one year. Charging cleaned sprue into a cupola reduces the required additives in some cases from 4% to less than 1%. This results in substantial savings in coke consumption, faster melting, less slag to handle, reduced deterioration of cupola linings, and easier cupola control. Cores from the shakeout / knockout can be processed with the sprue, releasing rods, gaggers, arbors and wires for picking.
Material can be loaded into the DUCTA-SPRUE® rotary mill in a variety of ways, then is subject to a tumbling action which removes the sand from the metal and breaks up large core lumps. The sand passes out through slots in the shell while the cleaned metal parts are discharged from the end of the barrel. Air is vented from the screen section, using air drawn in from the inlet and outlet of the barrel to prevent the escape of dust into the foundry.
Standard and Custom Sizes
General Kinematics offer standard as well as custom sized DUCTA-SPRUE® rotary drums. DUCTA-SPRUE® rotary drums employ steeply pitched helical flights at the inlet to advance the material into the cylinder, rapidly avoiding spillage over the feed end retaining ring. The main shell is provided with easy to replace wear resistant liner plates, and lifting bars which raise the material as the shell rotates, increasing the material tumbling effect. The riding rings are forged steel, supported on forged trunnion rollers. Thrust rollers and standard drive equipment are included with all models.
FEATURES:
Separation of sand, media, and tramp metal is done outside the rotating assembly on a GK vibratory processor, eliminating rotating mass and wear to the drum body.
GK fabricated liners are easier and safer to replace, and cost up to 75% less than cast grid systems.
Patent-pending liner system eliminates compression rings, heavy cast liners, and excessive maintenance costs.
Drum shell is not a wear item, saving you considerable maintenance funds and headaches.
Drums use easy to source commercially available components.
Available in standard and custom sizes to match your process design and throughput.
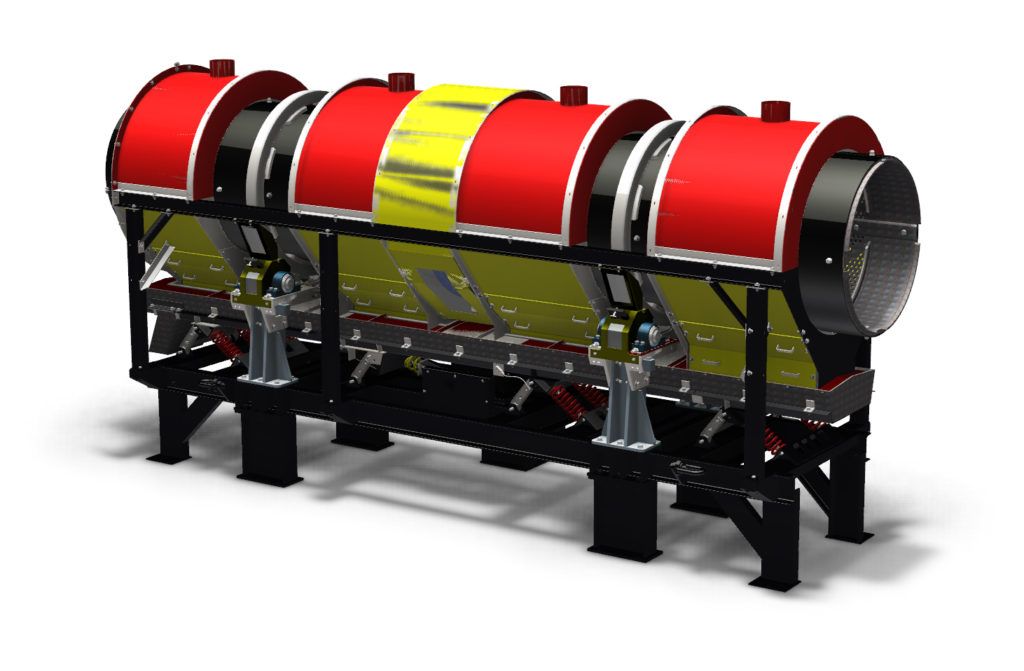
DUCTA-SCREEN™ ROTARY SHAKEOUT
The DUCTA-SCREEN™ rotary shakeout quickly and efficiently processes molds to separate and remove sand from castings. Sand is broken down, leaves the rotary shell, and is deposited on GK’s vibratory sand take-away conveyor. The removal of sand from the rotary shell allows cooler equipment temperatures, allowing for increased equipment and component life, and reduced casting temperatures.
The DUCTA-SCREEN™ rotary shakeout is an ideal unit for separating castings from flaskless molds. The self-contained unit reduces the noise and improves sand separation from castings and sprue. The action of the rotary shakeout is smooth, yet it efficiently breaks down sand lumps and provides sand suitable for very fine final screening. Standard and custom sizes are available to best suit your application.
Contact a GK Foundry specialist for more information.
GK fabricated liners are easier and safer to replace, and cost up to 75% less than cast grid systems.
Patent-pending liner system eliminates compression rings, heavy cast liners, and excessive maintenance costs.
Drum shell is not a wear item, saving you considerable maintenance funds and headaches.
Drums use easy to source commercially available components.
Available in standard and custom sizes to match your process design and throughput.
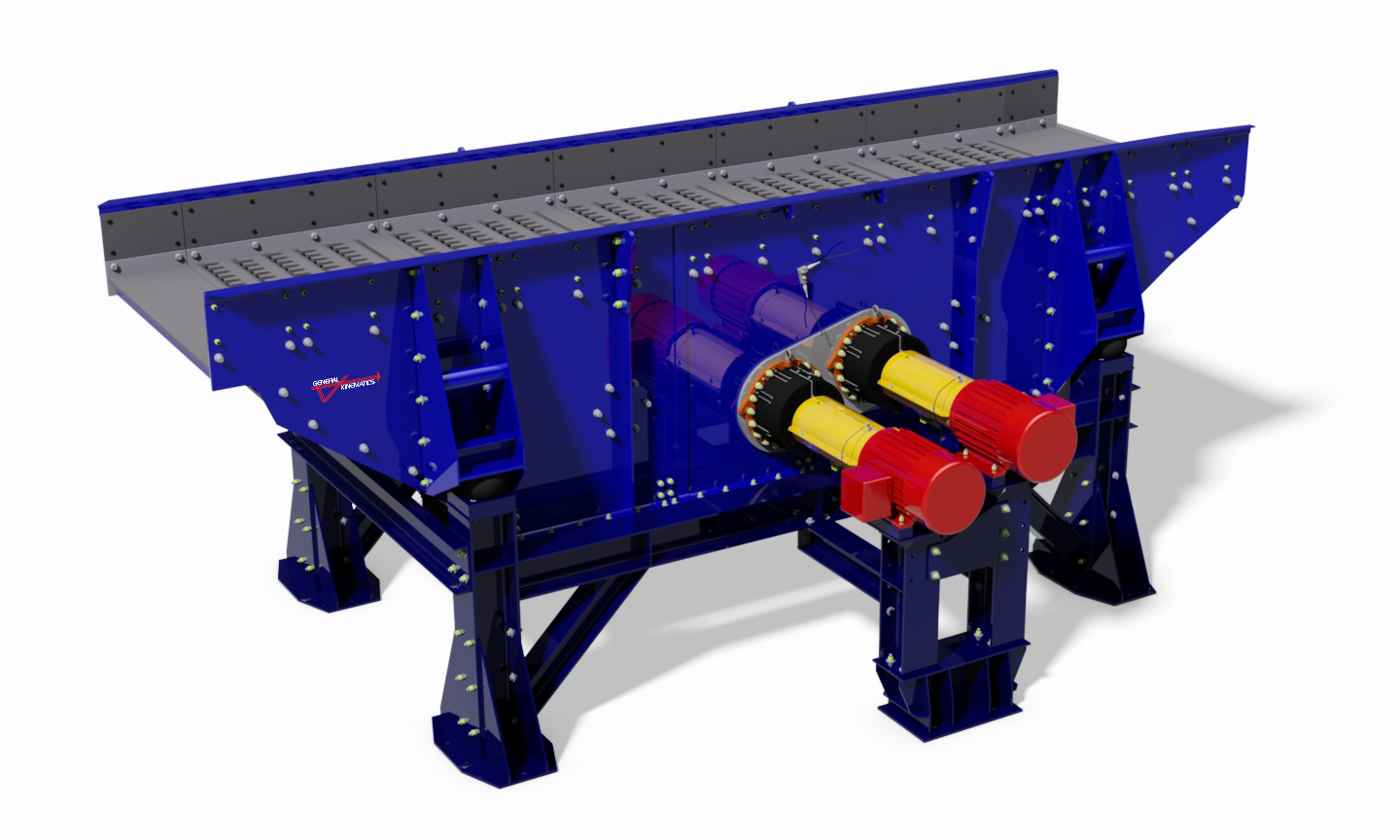
V2™ VARIABLE ANGLE SHAKEOUTS
General Kinematics V2™ Variable Angle Shakeouts allow you to adjust casting retention time with the push of a button. Long lasting components and extra heavy-duty construction offer extended uptime and low maintenance operation.
Direct drive design is simple to maintain and to install. The easy to operate control system of the V2 utilizes vector based measurement to monitor and maintain the proper shakeout angle for your casting type, as well as the ability to adjust travel speed to optimize shakeout time for various casting sizes and shapes. Operator controls can be located anywhere, including inside manipulator cabs, to allow operators to quickly adjust retention time to suit their process requirements.
FEATURES:
Easy to use operator stations allow quick adjustment of travel rate and retention time.
Vibratory drives are easy to service and even easier to replace.
Available in standard and custom sizes depending on your application.
Multiple units can be placed back to back for the ultimate in casting control.
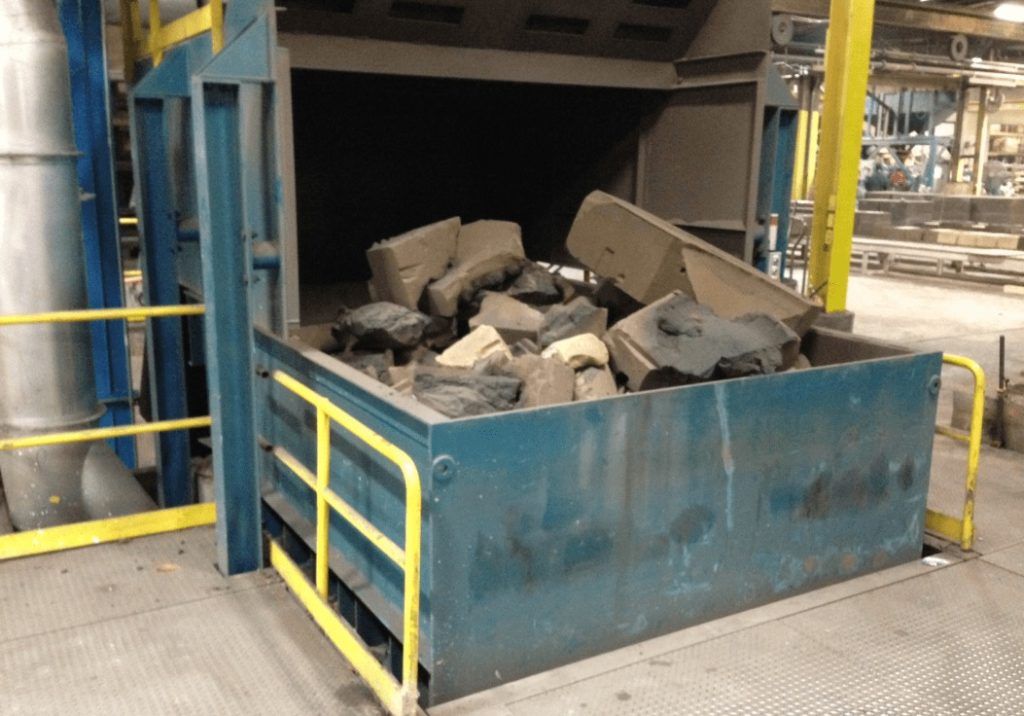
BRUTE FORCE / DIRECT-DRIVE SHAKEOUTS
From the inception of using vibration to shakeout castings, Brute Force Shakeouts have been utilized as an affordable solution to removing sand from castings. For over 50 years, GK has been perfecting this design, delivering a refined machine that is ready to work for you as soon as it is installed.
Used in simplicity of attaching two eccentrically weighted motors mounted directly to the vibratory mass, the General Kinematics Brute Force Shakeout makes your drive as simplistic as possible. For larger capacity systems, Two-Mass Shakeout technology is also available.
FEATURES:
Heavy-duty design for long service life.
An array of deck options available to best suit your process.
Designed for ease of service and low maintenance.
Available in various widths and lengths – contact our Foundry Specialists to find the shakeout that is best for your process.